Everyone from couture fashion brands to Girl Scouts have taken up mask making to fight the spread of COVID-19, with textile companies drawing on their unique capabilities to introduce new innovations.
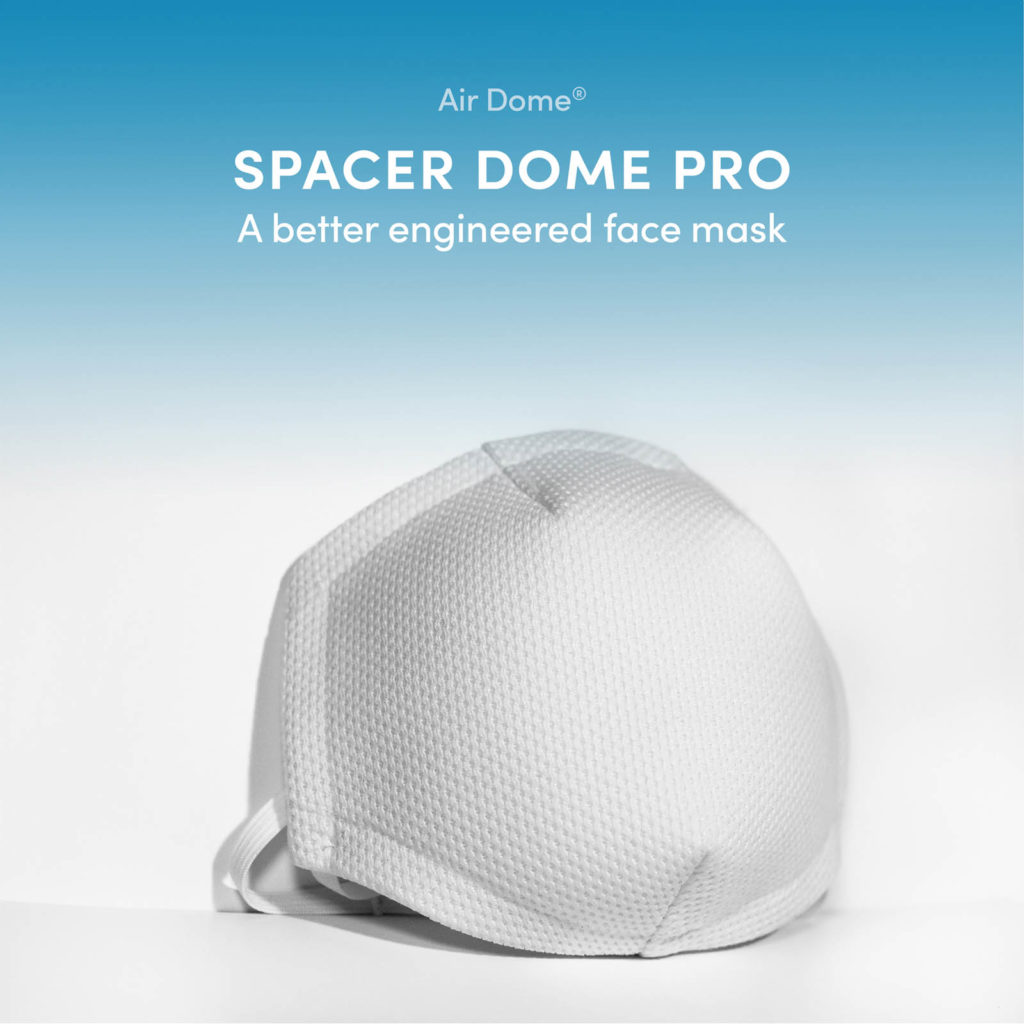
Patterned after N95 masks, the Spacer Dome Pro mask from Apex Mills, Inwood, N.Y., includes an air space that offers two benefits: the fabric stays away from the wearer’s lips, offering better comfort, and it allows the wearer to speak clearly and breathe easily. The combination of a three-dimensional spacer fabric and a tightly knit liner provides four layers of particle filtration, while remaining lightweight and foldable. The integrated pocket allows the wearer to insert additional filter media. The liner fabric is made with micro-denier yarns for enhanced softness and comfort, while the behind-the-head strap system is fully adjustable for a custom fit. Component fabrics, all made in the U.S.A., are antimicrobial and employ environmentally friendly, zinc-based technology.
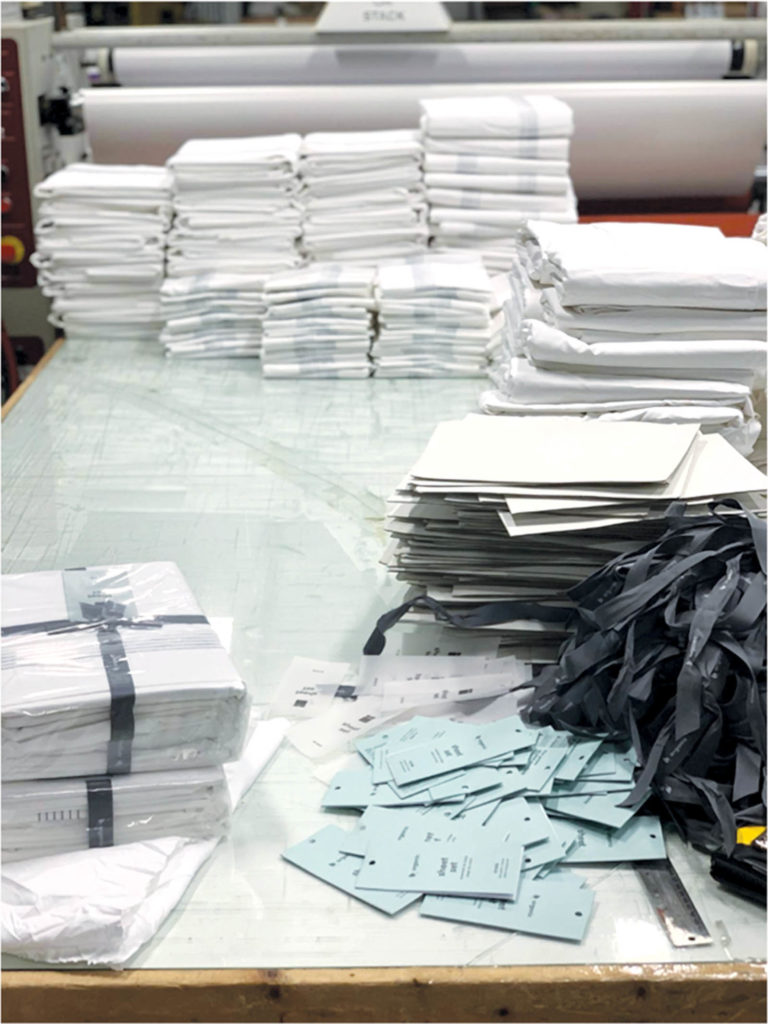
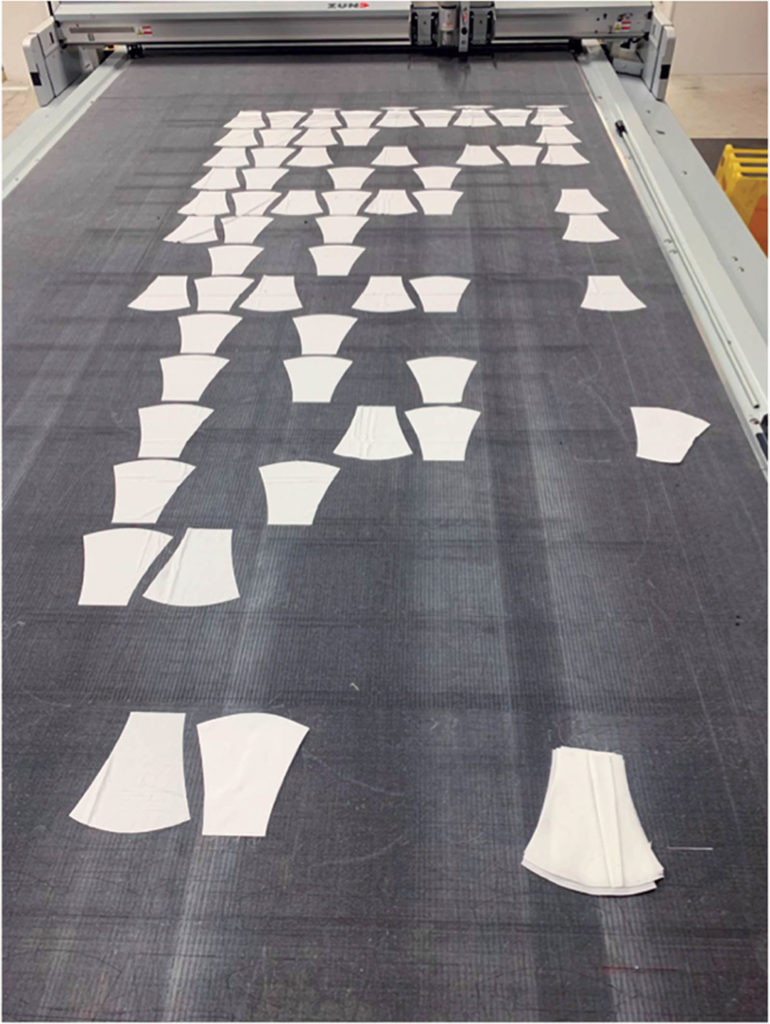
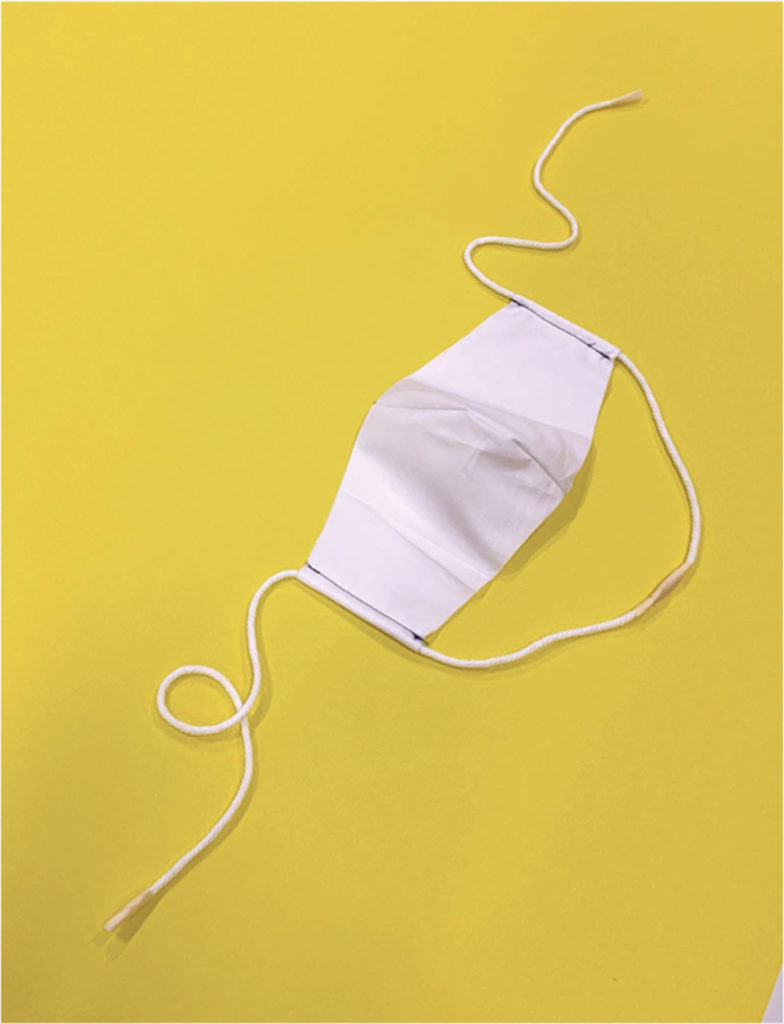
Pelican Wire, a manufacturer of application-driven wire solutions based in Naples, Fla., donated a large quantity of wire to ZSK Technical Embroidery Systems and BendShape, a wearable electronics company, for the production of “shapeable” face masks for front-line workers. “We’ve been working with the team at ZSK Technical Embroidery Systems, a division of ZSK USA Inc., on an e-textile product development program and continue to be impressed by the precise capabilities of their commercial embroidery equipment and the commitment to quality from their organization,” says Pelican Wire business development manager John Niggle. “When the opportunity arose to send some wire to ZSK to be used in creating a ‘shapeable’ mask, we jumped at the opportunity. It’s a privilege working with a company that puts such precision and care in their products and their people.”
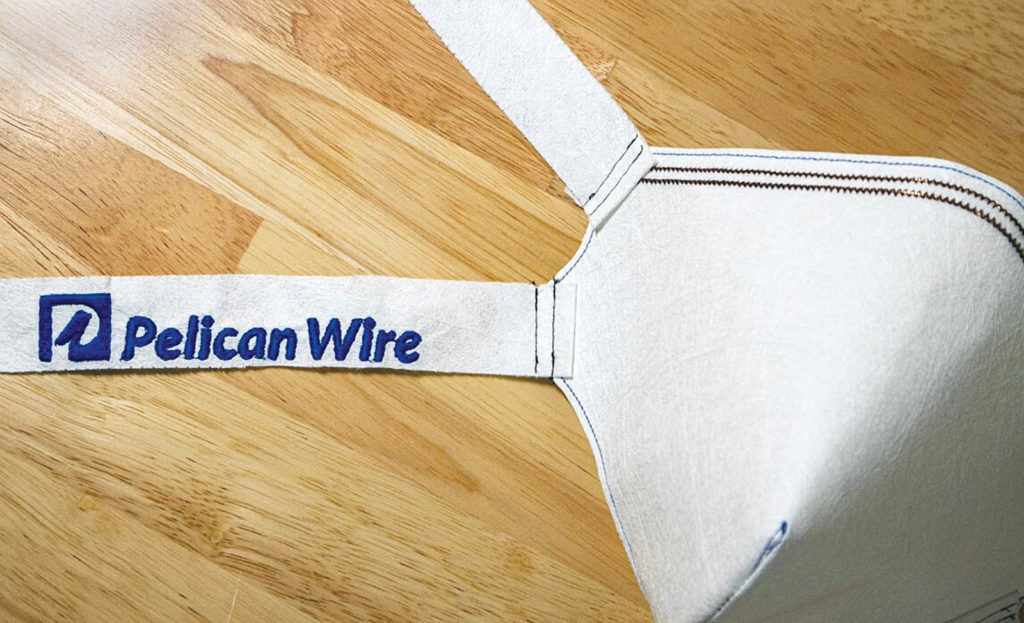
With a donation of 400-thread-count organic cotton sheets from furniture and home retailer West Elm, design firm Designtex set out to produce 13,000 face masks at its surface imaging facility in Portland, Maine. Each mask is made using two layers of organic cotton. With rotary style cutting on Designtex’s Zund G3 platform, production is quick, cutting close to 60 half-mask pieces in four minutes. Half-mask shapes are seamed to become full masks, and a sliding cord allows for fastening and an adjustable fit. When cord procurement presented an obstacle, Designtex slit its own strong and soft microfiber tie for safe and reliable fastening. The company is capable of producing 300 masks per shift.