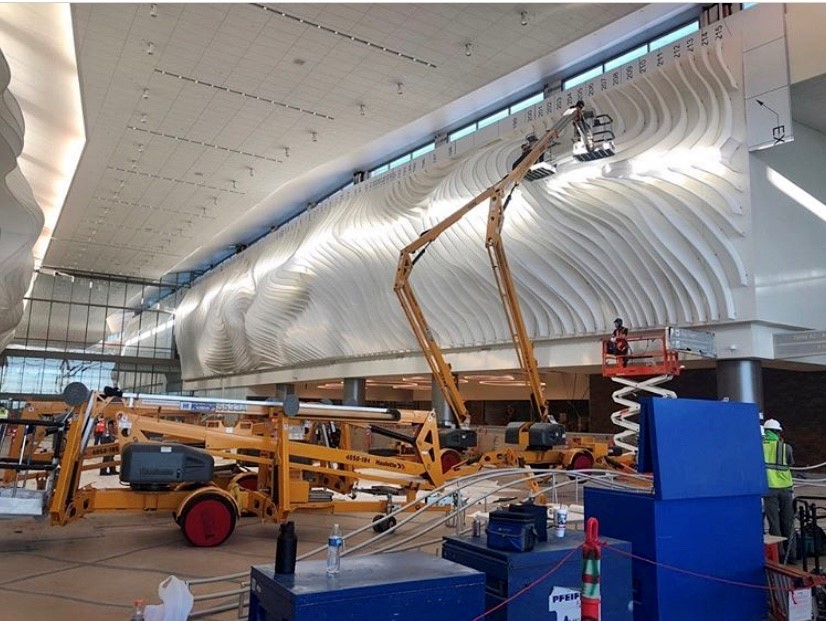
EDITOR’S NOTE: For the new terminal complex at the Salt Lake City International Airport, a specially commissioned public art installation involved architectural fabric. The visually stunning fabric sculpture “The Canyon” by public artist Gordon Huether was accomplished by a dedicated team of fabric engineers and fabricators who interpreted the artist’s vision. The scope of the project is examined in “The Art of Fabric Architecture” in the May 2021 issue of Specialty Fabrics Review.
Perhaps essential to translating this art into fabric was Charles Duvall of Duvall Design, Rockland, Maine. The installation, located in the main concourse of the newly rebuilt airport, is the dominant feature of that passageway. Duvall recognized that the art could be fabricated by hand but needed mechanical means to allow the work to be completed in time for the grand opening of the facility. Bruce Wright, FAIA, a frequent contributor to Review, spoke with Duvall after the installation was complete.
Bruce Wright: When it became clear that mechanical fabrication would be required to finish the translation of Heuther’s artwork into fabric, you, Rainier Display and Pfeifer FabriTec Structures discovered a 3D tube bending machine at the Tube and Wire show being held at the time in Dusseldorf, Germany. What was it about the machine that convinced you to use it to help fabricate the fins that make up the sculpture?
Charles Duvall: The Dynobend machine, from The Netherlands, is the only freeform machine capable of 3D bending with variable radii. The latest Dutch 3D freeform bending machine could only bend 30-foot radiuses, but for our purposes we needed to go from 30-foot down to 6-inch radii and anywhere in between over the length of a single tube, all with continuously varying radii, not fixed radii. The company engineers were very willing to work with us to modify their software and to re-engineer the machine itself so that the machine could accomplish these goals, as well as adapt their testing equipment that verifies the bends. We visited their shop in a number of visits over the summer to test various material alloys with different wall thicknesses during the software and machine development to accomplish this. They trained us to operate the machine. For me, this was hugely advantageous. Also, as a test, we produced a set of fins with fabric before leaving the Netherlands.
Wright: What were some of the challenges you encountered?
Duvall: There are over 9,000 unique pieces of tubing in this Phase 1 project. Each fin is composed of a distinct front and back with about 40 to 50 panels of fabric for each fin. The biggest challenge to the bending production was creating curves in Rhino [software] that don’t exceed the machine’s limitations for bending and rotation. This required a number of steps to eliminate anomalies in the curves using Rhino tools. Tube subdivisions are also critical.
To produce one piece of tubing there is a set of two files required, one for bending and a second for marking. Each piece has marks for alignment, name, bar code, drill and countersink holes. All of the marks are placed on the surface of the tubes in a drawing. There are about 15,000 marks total.
These digital files then had to be put into and configured for the fabric cutting patterns. These also had to account for a 3 percent biaxial stretch based on the type of fabric selected for the artwork.
Wright: What sort of fabric was used?
Duvall: The fabric is called Tweave® made by Gehring Textiles in the U.S., and is a FR-rated knitted fabric, with a mechanical stretch created with a crimped nylon yarn. Spandex wasn’t used because it would lose its stretch over time.
Wright: Was there any special computer code needed to control the bending machine; software to handle tubing?
Duvall: As to the tube bending, I worked with a software simulator creating “real time” virtual bending of pipes as a way of finding any potential technical problems before actually sending the files to the 3D bender to make each pipe in production. I simulated the manufacture of every pipe part twice before giving these files to the Rainier production shop.
Wright: What did you use for the pattern making?
Duvall: The fabric patterning was done in Mpanel to make sure the tubing and fabric worked together. And there were two sides that needed to be made for each fin, front and back. I look at it sort of like fitting and making a custom dress. The goal was to maintain simplicity of assembly despite the thousands of unique pattern parts. I used Mpanel in a way to achieve a three-dimensional shape in the radius curves of the frames rather than a simple two-dimensional shape so the final shapes are very organic, not flat.
Wright: You’ve said that Phase 2 has already been fabricated and is waiting in protected storage until the airport starts up construction later this year. Will Phase 3 be much like the first two phases with regard to fabric usage?
Duvall: Phase 3 will be an 800-foot-long by 20-foot-wide ceiling over the walkway in the tunnel connecting both Phase 1 and 2 terminals. So it will simulate a river instead of canyons. With all of the design, programming, debugging and fabrication experience under out belts, the last phase I feel certain will have a better degree of perfection in the end product.