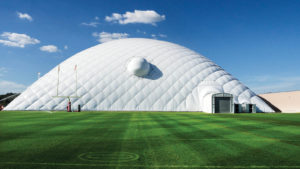
The Tennessee Titans debuted a new practice facility in the summer of 2016, replacing their former air structure with one much brighter, bigger and sturdier. After more than 17 years of use, the original facility, located at Saint Thomas Sports Park in Nashville, Tenn., was showing signs of deterioration, including dirty fabric, poor lighting, inconsistent temperatures and a weakened cable system. Among many requirements, in its new building the team wanted architectural appeal, structural stability and longevity, says Donato Fraioli, who manages technical sales and product development at Air Structures American Technologies Inc. (ASATI) in Rye Brook, N.Y.—the company that built the structure.
“To get an NFL contract like this takes a lot of time and planning,” Fraioli says. “It was a rigorous process; they shook everyone down.” But who better could relate to the “practice makes perfect” assertion frequently used in athletics?
Decades of discipline
A three-generation family business, ASATI had completed 13 NFL team facilities at the time and proved its successful history of building similar structures in short time periods—another important factor for the Titans, as the new facility was to be completed in just a few months in order to be ready for training camp. “Most of our spring training projects are for the fall, but we had to really be diligent about the timing of this one,” Fraioli notes.
The team also wanted more space—in height, specifically. Covering 88,592 square feet at 90 feet tall, 392 feet long and 226 feet wide, the new facility stands 20 feet higher than the original. This height-to-width ratio is not common to air structures, but ASATI was already well-versed in creating designs to provide the right amount of stabilization for a dome of this size.
“If you’re going to build a structure that’s worth X amount of dollars, it has to be built in a certain manner,” Fraioli says. “Everyone else can make bubbles, but we have the know-how to meet really specific requests.” His grandfather founded ASATI in 1962 and is responsible for many technical innovations used in the industry today.
Minimal stretch, maximal stability
One such innovation is the company’s full bias cable net system. Unlike the former structure’s coaxial cable system, the full bias cable net eliminates shaking in the wind and greatly reduces fabric loads in all directions, as they’re first transferred to the cable net system and then to the anchorage system. In extreme weather, fabric loads can be anywhere between 60 and 100 pounds per inch, or even more. The full bias system reduces the loads to about 6 pounds per square inch.
“You’re putting a lot of stretch on your fabric if you’re using no cable system or even a coaxial one,” Fraioli explains. “When the fabric is experiencing these heavier loads, you’re just barely scraping industry standards in terms of the safety factor and you can’t predict where and what those loads are across the building. If fabric is experiencing a heavy load, it will fatigue; if it isn’t, it doesn’t fatigue.”
The facility’s full bias system uses more than 125,000 square feet of 8028 fabric from Wooster, Ohio-based Seaman Corp.: opaque white for the side walls and translucent white for the skylight covering the field. Both are coated with bright white Tedlar®, a polyvinyl fluoride film from DuPont™ with powerful self-cleaning properties. The 8028 product is part of Seaman’s line of Shelter-Rite® architectural fabrics, which are engineered with a proprietary coating formula for UV and mildew resistance, and unique weft inserted knit fabric that provides tensile, tear and seam strength.
“For the design of this building, the 8028 was the right strength and the Tedlar offered the desired aesthetic and longevity,” says Frank Bradenburg, business director of architectural fabrics at Seaman. “Structures like these for the NFL are high-profile; they certainly don’t want their buildings to look shabby, and that’s really where the Tedlar is used. It provides the best aesthetics of any fabric out there.”
Lighting also played a role in fabric choice. “The skylight has an architectural appeal to it but also allows the natural light in during the day so you don’t have to flip your lights on,” Fraioli notes. “What’s also nice is that at night, an opaque building reflects the light off the ceiling and brightens the building up.”
The energy effect
The natural light enhances ASATI’s dome-specific LED lighting system—the first of its kind, which ASATI developed and first installed in a seasonal dome on the North Dakota State University campus. Made from
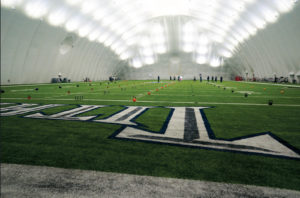
high-strength aluminum and acrylics, the lights reduce energy consumption and do not require bulb changes or ballasts, or break when hit. More than 100 lights are suspended from the ceiling, as are the goalposts, so they don’t penetrate the dome in the case of deflation.
To solve the former facility’s heating and cooling issues, ASATI implemented a triple-wall construction, increasing the building’s thermal value from R-4 to R-8. The company recommends this level to maximize energy efficiency, as it provides the largest insulation value while allowing the structure’s fabric to remain translucent.
Additionally, the energy-efficient HVAC unit ASATI installed features wind and snow sensor automated controls that increase building pressure and temperature in storm conditions. The unit’s heating system recirculates warm air, maintaining a constant ceiling-to-floor temperature, which decreases heat demand.
Playing to plan
The structure was built over the same spot as the previous dome and attached to the existing concrete beams. “It was a bit tricky because we had to install over their brand-new turf,” Fraioli recalls. “We had to be very careful about how we drove machinery around the site, where we placed the bundles; it took a lot of planning.” The players used an outdoor field temporarily, though deflating the old structure and inflating the new one was only a several-week process, Fraioli says. He expects the building to last for at least 20 years.
Though both air structures and Shelter-Rite fabrics are often used for athletic applications, Fraioli is set on increasing public knowledge about their advantages. “The Achilles’ heel of our industry is that we don’t create our demand because the air structure is so useful and so few people know about it,” he says. “We’ve been growing the industry organically from structure to structure, but I think there’s so much more that can be done, far beyond just sports.”
“Air structures are still the most economical way of making a large clear-span building,” Bradenburg adds. “It’s been a very interesting business to be in. Over the years there’s been more and more demand for longer-lasting products, and some new requirements are coming down the road that may require stronger fabrics.”
Holly Eamon is an editor and writer based in Minneapolis, Minn.