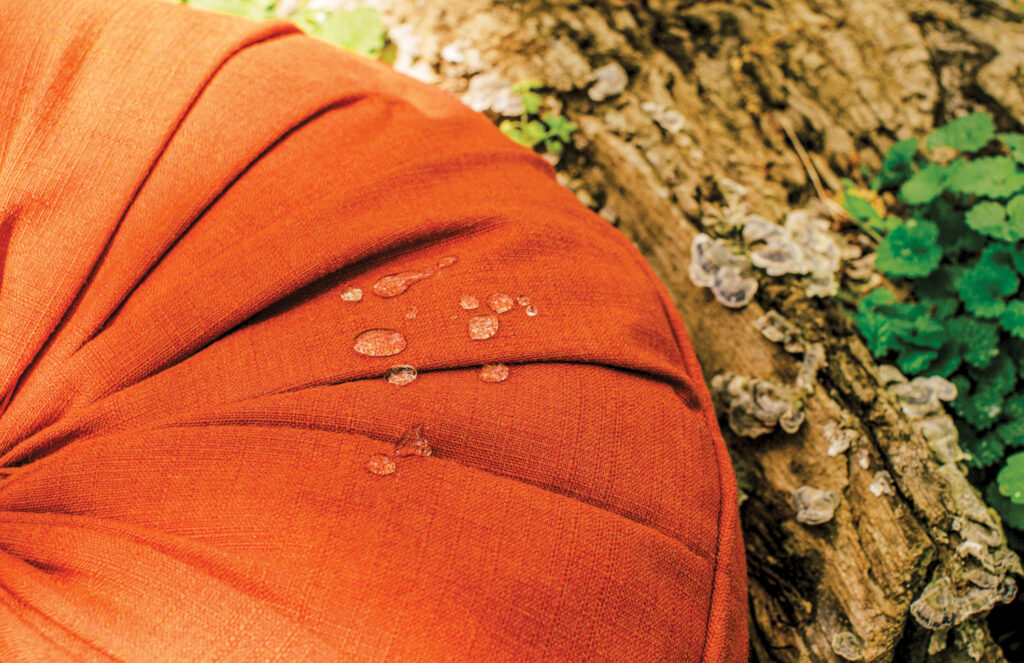
As the momentum to eliminate per- and polyfluorinated alkyl compounds (PFAS) picks up speed, growing numbers of product manufacturers and suppliers are exploring how to make their lines comply with the ever-tightening regulations and restrictions affecting C6 PFAS (long-chain C8 chemistries are already widely banned). Included among these are providers of durable water repellent (DWR) textiles, fibers and/or finishes. For years, these companies have utilized PFAS to repel a variety of substances such as water, stains, oil, food, dirt and bio-fluids, among others.
But as concerns over PFAS and their impact escalate, many companies have been researching and adopting fluorine-free DWR options and transitioning away from C6—a shorter-chain PFAS that was considered a safer alternative to C8 but that studies now indicate might be similarly persistent and toxic to the environment and to human and animal health.
This shift could prove prescient as more states appear poised to ban PFAS-containing products—an action affecting textiles, food packaging, leather, carpets, upholstery and so on, unless it can be documented that no other reasonable alternatives exist. In the following, we look at three DWR providers who have undertaken this effort and consider their results so far.
Imitating natural repellency
For more than 15 years, Schoeller Textil AG has been working on its C0 fluorine-free DWR finish, becoming one of the first to bring a solution to market that eliminates the toxins associated with C8 or C6 DWRs, says Stephen Kerns, president of Schoeller USA. Headquartered in Sevelen, Switzerland, Schoeller Textil AG develops and manufactures functional fabrics and textile technologies for markets including outdoor, athletic, fashion and workwear, with sustainability among the company’s primary focus throughout the entire production chain.
Ecorepel® is its leading C0 finish, says Kerns, explaining that it’s been available in different formats for 14-plus years. The perfluorochemical or PFC-free and bluesign®-approved solution mimics plants’ natural protection via a “high-performance, permanently odorless, high-tech finish” that wraps a thin film around the fabrics’ fibers, acting as a repellent, enabling water droplets and aqueous dirt to run off the surface, he explains.
“We are now on a 3.0 version that can provide durability of 95% spray ratings after multiple launderings,” Kerns says. “We are unique in the sense that we are the only mill-based technology company, which allows us constant trials and efforts, all on the premises in our R&D department at Schoeller headquarters.
“Applications across numerous compositions are more challenging,” he continues. “Being a Swiss company, we are preoccupied with showing what is possible first and not showing simply what is good enough for many.”
According to Kerns, the C0 solution compares favorably to C6 finishes in initial spray ratings and durability after multiple launderings. Where issues remain is oil repellency, such as stains caused by anything from foodstuffs to petroleum (“Still tough to offer in C0 for all types,” he says). Blood-borne pathogens are another concern.
Consequently, although some of Schoeller’s bluesign-approved C6 legacy products have been converted to C0, others—such as those developed for the first responders and protection categories—remain C6 since these end users require “ultra-protection” that C0 finishes can’t achieve.
As for what lies ahead for C0 DWRs, Hans Kohn, chief operating officer for Schoeller Textil AG, anticipates performance and durability improvements.
“C0 DWRs will be more dedicated and adjusted to the individual end use,” Kohn predicts. “Oil repellency will continue to be a focus of development for some protective applications—for the wide range of end uses, this requirement will disappear over time.”
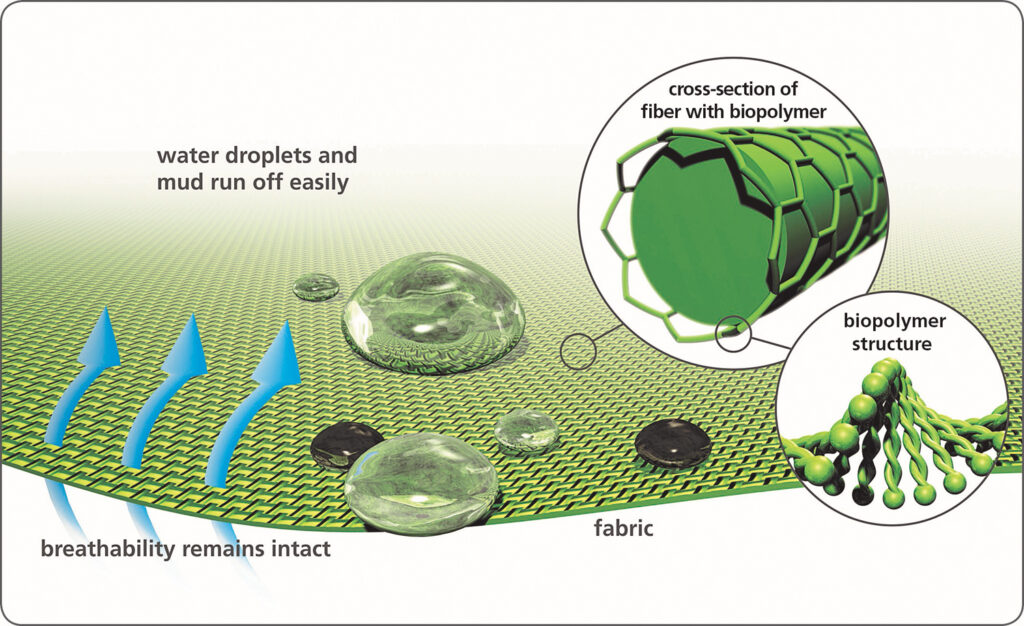
Successfully switching
In February 2023, Milliken & Co. announced it had successfully removed all PFAS from its textiles, fibers and finishes, making it the first multi-market U.S.-based textile manufacturer to do so.
Headquartered in Spartanburg, S.C., Milliken is a global textile manufacturer serving the industrial, automotive and apparel industries, says Jeff Strahan, Ph.D., director of research, compliance and sustainability, Textile Business, adding that the company has made operation-wide sustainability a key focus.
Its conversion to a non-PFAS portfolio began in 2022.
“For any customer that required a DWR finish on their fabric, we evaluated non-PFAS technologies, including but not limited to those from accredited organizations such as bluesign,” says Strahan. “That was a challenge for our team because not every non-PFAS DWR works in every application.
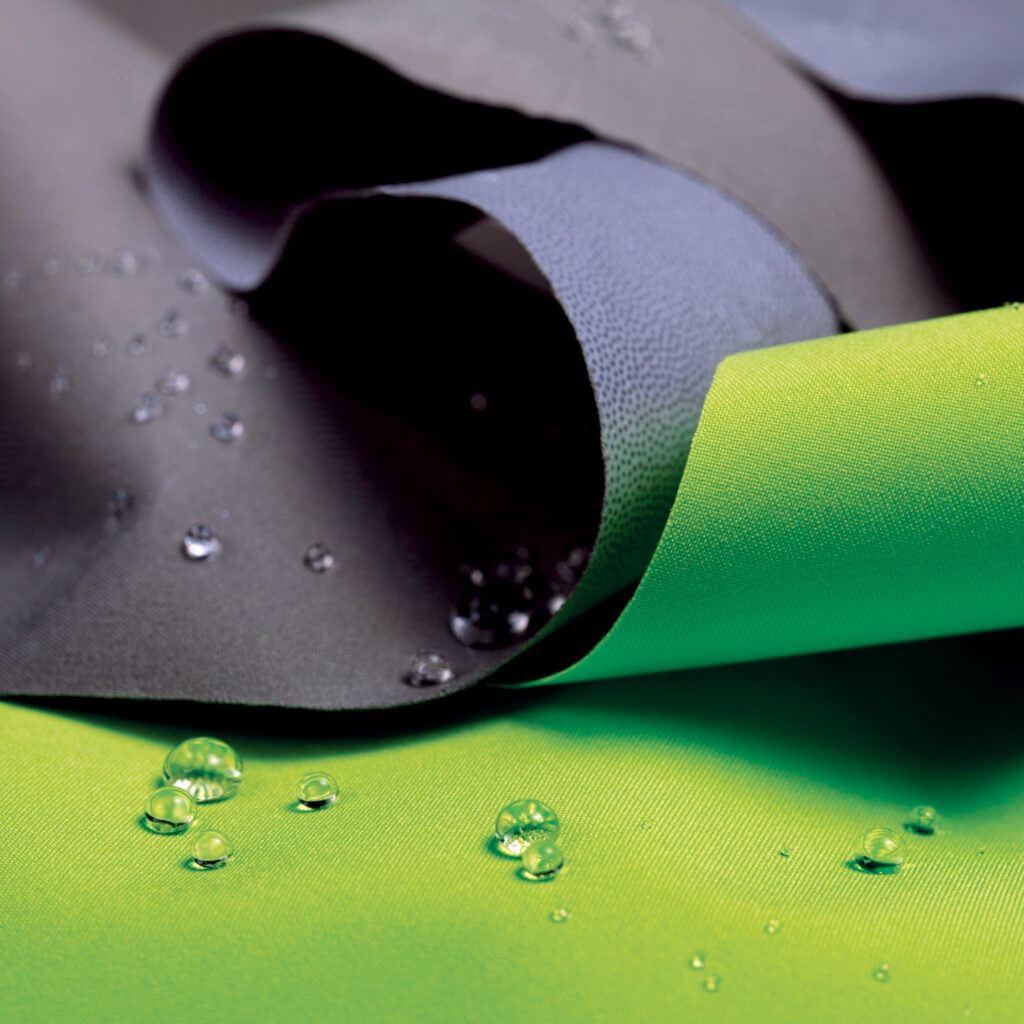
“We evaluated dozens of solutions across hundreds of products to ensure that every new, non-PFAS DWR had the same efficacy and functionality of the former PFAS options,” he continues. “The process of reviewing, vetting, selecting and application took our development team approximately 18 months.”
Ultimately, the company was able to find an alternative non-PFAS solution for every DWR application requiring one. For example, in 2022 the company’s decor team launched the Milliken Outdoor Fabrics line of non-PFAS performance fabrics, allowing the 100% solution-dyed acrylic fibers to “handle every weather element,” says Strahan.
Another example comes from Westex®: A Milliken Brand. At one time, the Westex AllOut® flame-resistant fabric utilized a PFAS-containing DWR. However, this was also successfully switched to an alternative non-PFAS solution.
Strahan says the company has been able to find non-PFAS finishes that meet customers’ performance and longevity expectations, even for those involving roofing materials.
“We are not seeing any application limits for DWR finishes at this time,” he says. “The biggest challenge is finding the best solution for the appropriate application. The solution exists, but you have to do the work to find the right solution for the product.”
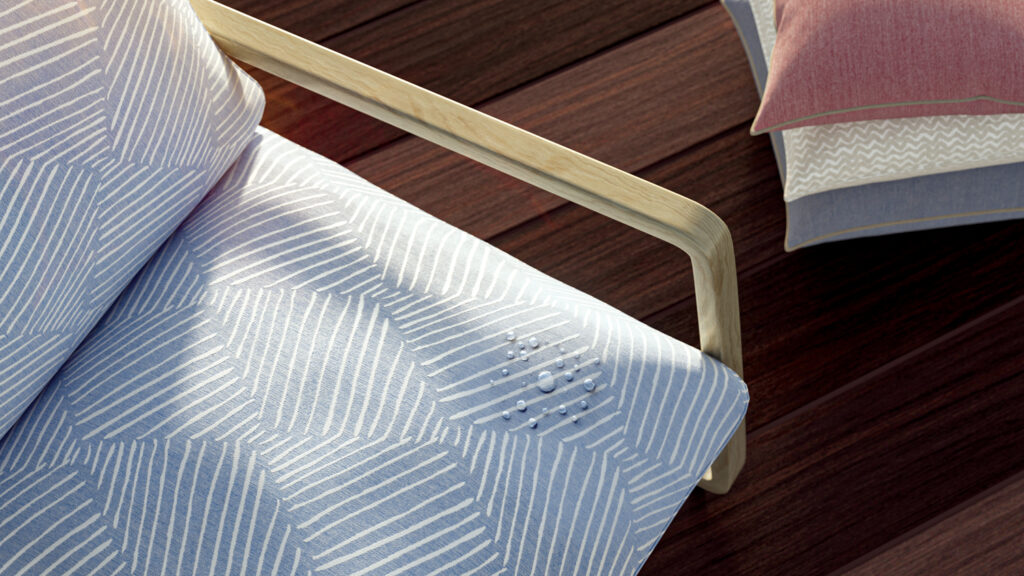
A primary objective
For the past five to seven years, removal of PFAS from DWR applications has been a primary company objective, says chemist Frank Keohan, senior technology manager for Bolger & O’Hearn (B&O) Inc. Headquartered in Fall River, Mass., B&O offers chemicals, paper coatings and nonwovens as well as non-textile manufactured items to a diverse range of markets. Keohan describes the company—a bluesign System Partner—as “committed to a zero-carbon future,” using renewable energy to manufacture its products.
Among the company’s fluorocarbon-free offerings is Shell-Tech Free M325-SC1, developed to meet the desire for a water repellent that is both durable and sustainable. The solution’s aqueous finish is based on a hydrophobic-reactive polymer, providing cotton-rich and synthetic fibers with high water repellency as well as outstanding wash durability, says Keohan.
Shell-Tech Free 6053 is another of the company’s high-performing, fluorine-free aqueous finish solutions and is designed to provide high water repellency to a variety of natural and synthetic fiber-based textiles. Altopel F3® is another such finish. This bluesign-approved product provides high water repellency to cotton and synthetic fibers including rayon, nylon, aramid and polyester.
It took almost two years for the original Altopel F3 to find commercial acceptance, says Keohan. The Shell-Tech Free products are a more recent effort, requiring at least a year of laboratory work from the technical staff before being trialed by B&O’s customers. Currently, the M325-SC1 grade has been commercialized; the 6053, developed in the last year, is in customer trials.
Fluorine-free DWRs compare favorably to fluorochemical-based ones in terms of water repellency, says Keohan. They also offer good stain resistance to things like mud, fruit juice, wine, syrup, soda and other “stain-causing materials having a continuous water phase,” he adds.

“[Consequently], many if not most clothing brands and finishing mills whose products do not have oil repellency specifications that some military and medical products must meet have already shifted to fluorine-free products for water repellency,” says Keohan.
“Where oil repellency is demanded, only fluorochemical repellents will provide the necessary performance,” he adds. “We do not see this situation changing anytime soon.”
Keohan believes the shift away from PFAS-based repellents and soil-release finishes will continue, potentially changing how textiles that once demonstrated good oil and stain resistance via fluorochemical-based finishes perform.
“For example, consumers of winter outdoor apparel will notice that their coats, while exhibiting water repellency, might pick up oily stains where they didn’t in the ones purchased a few years earlier,” he explains.
The technology behind fluorine-free DWRs will make progress, especially in the areas of wash durability, degree of repellency, biodegradability and bio-based content, says Keohan, who anticipates some progress as well as in the ability to repel more stains and fluids of a “nonpolar” nature.
“However, we do not feel that fluorine-free repellents will be able to match the level of oil repellency imparted by current short-chain fluoropolymer-based products,” he says. “We also predict that the standards of some applications that still require oil repellency, such as military apparel and medical, may see some relaxation or at least outside pressure for relaxation. How this manifests itself will strongly influence the demand for PFAS-based repellents.”
Pamela Mills-Senn is a freelance writer based in Seal Beach, Calif.
SIDEBAR: Does fluorine-free mean earth friendly?
Is the assumption that PFAS-free DWRs are more eco-friendly and have better end-of-life recyclability than their PFAS-containing counterparts a valid one? Based on the following responses to that question, the answer is yes … potentially.
“The current class of fluorine-free DWRs are significantly more eco-friendly than fluorochemical-based products by the simple removal of PFAS. In addition to the absence of fluorine, some new DWR chemistries have significant biomaterial content, improved biodegradability and less overall toxicity. For example, fluorochemicals present significant inhalation and aspiration risks to handlers, which reduces their ability to be applied by spray. The new fluorine-free DWRs thus would allow broader application methods.”
Frank Keohan, Senior technology manager, Bolger & O’Hearn
“In general there are no major DWR-specific components in C0 DWRs which disturb a recycling process. But on the other hand, we have to look at the recycling process itself (mechanical, chemical, pyrolysis) and its specific requirements. The industry is still in a learning curve regarding these requirements.”
Hans Kohn, Chief operating officer, Schoeller Textil AG
“The term ‘eco-friendly’ is ripe for greenwashing, so I will restate: We don’t see any regulatory, supply chain or market pressure on our new DWRs. Most textiles do not have a wonderful end-of-life story. This has been well-documented by others and by many people working on it, including Milliken. With regards to our new DWRs, they do not negatively impact the end-of-life recyclability of the underlying textile.”
Jeff Strahan, Director of research, compliance and sustainability, Textile Business, Milliken & Co.