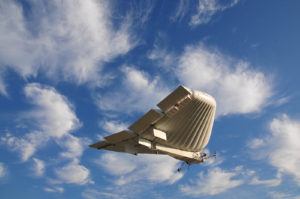
Carving out new niches in a stable industry
What could possibly be new in the cargo control and packaging industry? Aren’t containers, pallets and trucks the same as they’ve always been? Isn’t the goal always to secure items to transport them from point A to point B?
The basics may be the same, but the details are always changing. One trend that’s starting to show up is the use of SD (static dissipative) materials to protect electronics. It’s common in applications such as industrial curtains—especially around server rooms—but it’s likely to spread to many types of cargo-related applications since a charge imbalance can impact the performance of sensitive devices.
For a while, says Mark Deutsch, president of AmCraft Manufacturing Inc., Elk Grove Village, Ill., reducing weight was one of the major drivers in shipping container innovation. That leveled off eventually after a large-scale influx of inflatable package fillers and lightweight plastic containers.
Now the emphasis is more on eco-friendly packaging and shipping materials. Deutsch says he’s seeing more reusable shipping containers throughout the industry.
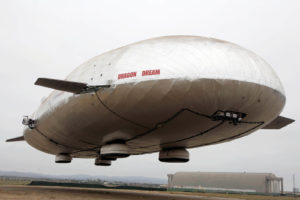
That doesn’t come as a surprise to Rob Jones, eastern region sales manager for industrial textile products at ABC Industries, Winona Lake, Ind. His company manufactures laminated fabrics for a variety of industries. One growing portion of ABC’s business is returnable packaging fabrics that are used primarily in totes and racks for the automotive industry. These racks are used over and over as long as the same automobile models are on the market. When the models change, so do the totes, racks and returnable packaging fabrics. ABC provides the needed fabric to cut-and-sew shops, and the cycle begins again.
“Any mass-assembly environments involving finished components, such as electronics, appliances and motorcycles, often utilize returnable packaging products,” says Jones, but the automotive industry is a huge market driver due to its sheer size. Seasonality has been an issue, with demand spiking when new models come out late in the year. Now, new models are coming out earlier in the calendar year, spreading the demand and making it easier for the industrial fabrics industry to respond.
The fabric itself is more or less the same: PVC-reinforced laminate. Quality control and continuity remain critical for customers when they select a supplier. “The product consistency has to be there because you never know when an auto company is going to make a model change, whether they’re going to change it in two years or eight years,” Jones says. “Let’s say the bags wear out in five or six years and the same model of F-150 is still being produced. The OEMs want the cut-and-sew shops to make repairs or replacements for the existing program. They want to use a consistent fabric, and they’ll probably use the same shop that made the originals so they can be sure it will fit into their program.”
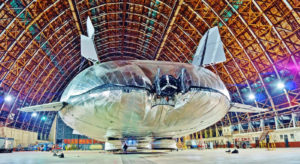
Quality control and continuity are also key to the continued success of tarp shops, says John Beule, sales manager at Harp’s Tarps, Tucker, Ga. The tarp market is lively right now, thanks to lower gas prices and an increase in construction activity. Yet competition is extremely fierce because there is a steady supply of premade tarps from around the world.
One solution? Make custom tarps. Beule says they continue to be a good product, and they provide an additional avenue to connect with customers. Another solution is to position the shop as a top quality provider.
“It comes down to who’s making the tarp and the techniques they use,” says Beule. “When we build a tarp, it’ll last two times, sometimes four times longer [than competitors’ tarps]. So our buzzword is ‘total cost of ownership.’ Our tarp may cost more up front, but if a guy has to replace his tarp once a year, or if he can’t pick up a load because the tarp’s torn, or if he has to do multiple repairs in a year, that’s going to be more expensive than the up-front cost of one of our tarps.”
Right for flight
As fabricators like Beule will be quick to point out, the transportation industry has a complicated relationship with industrial fabrics. On one hand, the shops make products such as tarps, straps, cargo webbing and bulk bags specifically for that market. On the other hand, the margin on the products these fabricators produce is greatly dependent on the current cost of fuels and the ease or difficulty of transporting fabrics and other materials to their shops and to customers.
It should come as no surprise, then, that makers of fabric products are entering a new sector of the cargo transport industry: not just securing goods while they are in transit, but actually moving goods in a more efficient way. Fabric is a relatively light construction material and can be made very strong and thin, so it’s a natural choice for air transport, where management of weight is crucial.
Lighter-than-air vehicles, often called airships or dirigibles, have always had the potential to solve cargo transportation problems, but historically they were limited by the need for tether masts or hangars wherever they landed. If 10,000 pounds of cargo was unloaded from them, they’d suddenly be 10,000 pounds too light and would, in the words of Aeros mechanical engineer and project manager John Wertz, “bob up like a cork.” So they required significant infrastructure including pre-deployed external ballast.
That problem limited where airships could go and what market share they were able to capture. But now two companies are addressing the buoyancy problem in ingenious ways, making fabric-skinned cargo aircraft a possible wave of the future.
Wertz’s company, Aeros, based in Montebello, Calif., has tested a rigid-structured cargo airship and is gearing up for the production of two commercial Aeroscraft cargo vessels: the ML-866, with a 66-ton payload, and the ML-868, with a 250-ton payload.
To solve the landing and offloading problem, the company has taken a cue from the buoyancy management systems used in submarines.
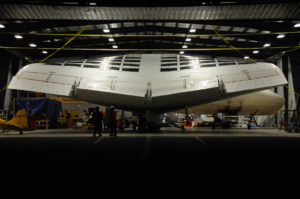
Photo: Solar Ship Inc.
“The biggest way we handle that is with our COSH system,” Wertz explains. “COSH stands for ‘control-of-static-heaviness.’ In a standard airship, you fill it with a certain amount of helium and that’s the amount of buoyancy you’re going to have no matter what. With the COSH system, we control our buoyancy by taking the helium and compressing it into containment vessels. Then we take the extra volume that is left over from the compression and pull air into special bladders within the airship.”
The COSH system lets Aeroscraft ships take off and land vertically, anywhere at all, with their maximum payload. The ships have vast, soccer-field-sized cargo areas (220 and 380 feet long, respectively), allowing goods to be loaded and unloaded in any order.
“The origin of our cargo airship came about through the military, but we feel it will have a number of commercial cargo applications, primarily in the industrial sectors—moving what’s known as project cargo, the larger and bulkier items that are very difficult to move either intermodally or to places that don’t have fully developed infrastructure,” says Wertz. “One area where we’ve gotten interest is wind turbines. A lot of the blades can’t be transported by ground-based systems because they are just too large. With an Aeroscraft, we can take huge blades to basically anywhere in the world and drop them off. We don’t even need to land; we can just lower them from the bottom of the ship.”
The materials are similar, but not identical, to those used in more traditional cargo control products. Fabrics range from high-tensile polyester to Vectran®, Spectra® and Dyneema®. Anti-UV coatings protect the outside panels and Mylar linings prevent helium from leaking through.
“We’ve used polyurethane aliphatic coatings on certain applications,” Wertz says. “It all depends on what the application is, whether it’s helium retention or just structural.”
Toronto-based Solar Ship Inc. handles the buoyancy problem in a completely different way. The company was founded with the mission of delivering goods to landlocked countries such as Burundi where fuel is scarce, roads are often unusable, there are no waterways and airfields are nonexistent. A hybrid aircraft that gains lift from both buoyant gas and aerodynamics with the ability to land on a piece of land as small as a soccer pitch was the answer. The company has a range of aircraft under development.
“Effectively, what we have is a large inflatable wing,” explains Stephen Wallace, Solar Ship’s lead fabric designer. “Our aircraft requires aerodynamics to keep it aloft. Because we fill the volume of the wing with a lighter-than-air gas, it means we’re getting buoyant lift as well. But the Solar Ship is designed so that it is always heavier than air; when it slows down, it is coming down. Once it has landed, it stays on the ground.”
The combination of aerodynamics and lighter-than-air gas means the Solar Ship can be designed to a mission-friendly “sweet spot”; for example, one where solar panels are sufficient to power it and, because the wing is large and flat, there is plenty of room for the panels.
“Ultimately, we would like to be fossil fuel free, not necessarily for environmental reasons, although that’s good, but because there are certain parts of the world where it doesn’t matter how much money you’ve got, you’re not getting fuel,” Wallace says. “So to have an aircraft that is divorced from the need for fossil fuel means you can actually move stuff.”
Currently the Solar Ship is made of a woven textile, which uses a high-strength fiber. It’s coated on the inside with a gas barrier and on the outside to prevent UV and environmental damage.
“We have some internal structure as well, which has different demands on the fabric,” Wallace says. “We don’t need the UV or gas barrier on those, so we’re coating those for weldability. The majority of our joints are welded, so all our coatings have to be thermoplastic. There are some sewn-in details, but on the whole, most of the structural joints are welded.”
To be compatible with existing transport networks, the Solar Ships are able to transport standard ISO shipping containers. The tradeoff is that metal containers are heavy, so part of the ship’s fuel is spent transporting the container. In the future, the containers, too, may be fabric or other lightweight materials.
How soon will it all happen? Solar Ship is testing its latest aircraft (and biggest one yet) at the end of the first quarter of 2016. It might be a stable market overall, but the winds are changing for everyone.
Jamie Swedberg is a writer and editor based in Woodville, Ga. For contact information on the sources used in this article.
A strategy for a stable market
For markets in which products are relatively straightforward, resistant to change and often price-driven, such as shipping and cargo containment, product diversification can be essential for supplier survival. But in order to succeed with this strategy, companies must expand the product lines that play to their core competencies.
For ABC Industries in Winona Lake, Ind., returnable packaging fabrics make up only a portion of the company’s business; other industrial fabrics serve industries ranging from recreational vehicles and industrial curtains to tents and athletic mats. What ties all of these fabrics together is their laminated construction.
“From our perspective, if it’s a laminated fabric, then we want to be a part of it,” says Rob Jones, eastern region sales manager for industrial textile fabrics at ABC Industries. “If it’s just a nonwoven, such as something where they use a spray adhesive to attach [the fabric] to a piece of corrugated plastic in a tote—something that requires no lamination—it’ll probably be something that happens without our involvement.”
The company is uniquely positioned in the laminated fabrics market, however, because it owns the entire process. “We make our own scrim reinforcement and produce the finished fabric in-house,” he explains. “We’re a vertically integrated company, which is our main advantage over others.”
So when fabricators are looking to produce the next big cargo control product, says Jones, they know who to contact if that product calls for a laminated material.
Similarly, AmCraft Manufacturing Inc., Elk Grove Village, Ill., specializes in products that combine RF welding or heat sealing with industrial sewing. The company makes cargo control solutions that range from industrial tarps to water, fuel and chemical bladders. Since 2012, one of its fastest-growing businesses is industrial curtains.
“We fabricate all of our products in-house, specializing in thermal and acoustic barriers for commercial and industrial customers,” says president Mark Deutsch. “The industrial curtains are the most significant part of our business. That segment continues to experience steady growth, and we have been directing substantial resources to marketing that product line.”
It’s a perfect storm: making industrial curtains relies on the same sewing and welding expertise that has made AmCraft successful in cargo transport. Market challenges continue to develop, however.
“I believe the competition relative to industrial curtains will be increasingly intense as more companies continue to diversify,” Deutsch predicts.