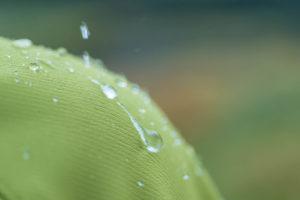
A closer look at environmentally preferred DWR finishes.
With the growing emphasis on multiple functionality and comfort in safety apparel, breathable and durable water repellency (DWR) has become an important attribute of most safety clothing and workwear.
Uniforms and workwear coated with PVC (polyvinyl chloride) or its greener alternative, polyurethane, successfully repel water, oil, dirt, chemicals, blood and airborne pathogens but they are hot, heavy and do not breathe to allow perspiration to pass through to the outside. This can create further hazards, such as heatstroke or exhaustion.
Since the development of DWR textile finishes based on PFCs (perfluorochemicals) in the 1950s, the lives of first responders, military personnel and outdoor industrial workers have been made safer and more comfortable.
Applied to the face of outerwear fabrics, DWR finishes prevent the fabric from “wetting out” without inhibiting breathability, making them especially critical for the functionality of the waterproof breathable laminates used as barrier fabrics in much of today’s safety apparel and footwear.
“DWR plays an important role across the end use applications of our technical fabrics,” says Amy Calhoun, public affairs communicator at W.L. Gore & Associates Inc., Newark, Del., which supplies the makers of military and safety equipment through its protective fabrics division. “For example, in fire turnout gear and military apparel, DWR can dramatically reduce the extra weight burden that occurs when fabrics are wet. This not only impacts the comfort of the individual, but their performance as well.”
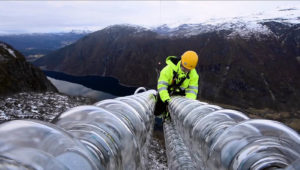
Transitions
The most effective DWRs are those based on PFCs using eight carbon atoms, referred to as C8 or long-chain chemistry. However, these PFCs contain perfluorooctane sulfonate (PFOS) and perfluorooctanoic acid (PFOA), substances that have been found to be toxic, persistent and bio-accumulative.
Most of the outdoor industry is transitioning into short-chain chemistry, or C6 compounds, which do not contain PFOS or PFOA, and break down more readily in the environment. Many are also pursuing the development of PFC-free alternatives in conjunction with the chemical and technology suppliers.
The textile and technology suppliers for safety apparel and workwear are also making the transition into C6 fluorine compounds. For example, Helly Hansen Workwear eliminated all C8 treatments from its production in 2014; and Gore Fabrics eliminated all PFOA from its supply chain for its ePTFE-based Gore-Tex® laminates in 2013.
While there have been some complaints that C6 technologies are less durable or require a higher rate of application than their C8 counterparts, most textile companies confirm that comparable efficacy can be achieved via a learning curve.
At Gore, the transition to C6 DWRs “was accomplished without a need to increase the amount of chemicals used in the application process or compromising the repellency performance end users expect,” says a company press release.
Lisa Hardy, North American marketing manager for Teflon™ textile finishes at The Chemours Co., Wilmington, Del., says of the company’s Teflon Shield C6 fabric protector, “It’s not a drop-in replacement. It may take some recipe adjustments or cleaner fabrics or, as a last resort, more product.”
According to Chad Kelly, global product and brand manager for eVent Fabrics, Kansas City, Mo., the ePTFE membrane manufacturer is “fully transitioning into C6-based DWR treatments.
“As we grow our business in the workwear market and introduce new technologies, we will also meet the demands of that market, which, I expect, with time, will also find that moving to C6 treatments will not compromise performance in workwear,” he says.
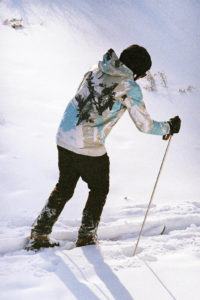
Alternative solutions
Questions remain regarding the safety of C6 compounds because they also contain PFCs that can accumulate in the environment. With NGOs such as Greenpeace pushing to eliminate fluorine-based DWRs entirely, technology companies are digging deeper into the development of PFC-free alternatives. These are based on various technologies, ranging from paraffin or silicone applications, to nanotechnology, plasma treatments and biomimetic, multibranched dendrimer structures.
The key to the performance of all DWR finishes is that they lower the surface tension, or adhesion, of the fabric, changing the angle of contact between a drop of liquid and the textile surface. The greater the differential between the molecular energy of liquid and the surface, the more the fabric repels the liquid. Liquids such as water have a higher molecular energy and are easier to repel than oil or chemicals.
The bottom line is that nonfluorine DWR formulations do not lower the molecular energy of the textile surface as efficiently as those based on perfluorinated compounds. While non-PFC treatments may offer adequate resistance to rain for the outdoor industry, their performance thus far has been subpar when it comes to protection against oil, dirt, chemicals, blood and other substances that might impede the efficacy of a textile laminate in safety clothing.
The PFC-free ecorepel® DWR finish by Schoeller Technologies AG, Sevelen, Switzerland, has been well accepted in the outdoor industry. However, Schoeller is not currently promoting its use in safety apparel and workwear.
“At this time, and for the workwear market, PFC-free finishes are not often in demand. One of the requirements for workwear is the ability to repel oil-based substances and so far it is not possible to achieve this without PFCs. Short-chain DWR finishes are state of the art today,” said Dagmar Signer, marketing communications for Schoeller.
Fluorine-free Barrier Eco by HeiQ Materials AG, Bad Zurzach, Switzerland, has just introduced improved versions of its technology at the recent ITMA exhibition. However, HeiQ CEO Carlo Centonze says, “Generally using fluorine-free technologies in workwear is more difficult. Industries that are looking at soil release and easy clean rather than direct repellency can use fluorine-free DWRs. Still requiring fluorine are oil industry, fire fighters, [applications for the] army.”
At SympaTex® Technologies, Unterföhring, Germany, which has worked closely with Rudolf Chemie to develop nonfluorine Bionic-Finish Eco® finish for its membrane fabrics, the verdict is similar, according to business development manager Heather Santos. “Typically we do not use Bionic-Finish Eco for contract and work wear because the customer still wants oil repellency. We suggest the Bionic-Finish Eco if water repellency only is needed.”
Chemours’ Lisa Hardy concurrs, “The biggest difference today provided by short-chain chemistry, such as our Teflon fabric protector, vs. our nonfluorinated Teflon EcoElite™ renewably sourced finish, is that short-chain product repels oil and nonfluorinated does not. In workwear and likely safety wear, oil repellency is a key functionality needed and we think those applications will stick with short-chain products to maintain the benefit.”
Looking to the future
The quest for DWR applications that are sustainable as well as high-performing has become a holy grail. W.L. Gore recently announced that it will invest more than $15 million over the next five years to explore alternative DWR solutions with an improved environmental profile and comparable or better comfort and performance.
The safety apparel industry must work alongside its suppliers to ensure the timely development of appropriate DWR finishes for its customers. For first responders, military personnel and outdoor industrial workers, sustainability in apparel is desirable, but safety and performance are nonnegotiable.
Debra Cobb is a freelance writer with extensive experience in the textiles industry.