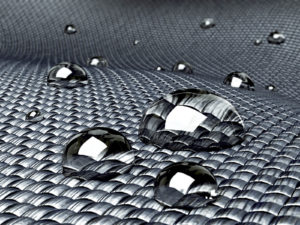
Perhaps the people who develop textile finishings by coating or laminating could best be described as the unsung problem solvers—superheroes, even—of the textile performance world. Do they wear capes? Maybe they should—textile capes finished with performance-enhancing treatments.
Problem solving is the basis of their work, as they treat textiles to enhance performance, in response to consumer demand. And they are unsung because much of the work they do is proprietary, with research carried out behind locked doors, often spoken of only in general terms to those outside of the written or verbal agreement. “We have been doing the same thing since 1901, which is taking somebody else’s textile product and making it better,” says Brian Rosenstein, CEO of TSG Finishing LLC, Hickory, N.C. “We don’t own or make any of our textile products. We work with just about every kind of textile product known to man, ranging from half-inch-wide ribbon for bedding to 160-inch-wide nonwovens for the medical industry, and everything in between.”
Industries that rely on coatings and lamination include aerospace, tenting, recreation, automotive, marine and apparel, health care and hospitality, among others. New and changing markets are always worth watching, however, and coatings and lamination providers work hard to stay abreast of current customer needs. “We expect aerospace and medical to grow faster than GDP, while [we expect] other segments to grow with the general economy,” says Steve Brockman, general manager for Trelleborg Engineered Coated Fabrics based in Trelleborg, Sweden. “As a well-diversified business, we work strategically to balance our current diversification with prioritized future growth investments.
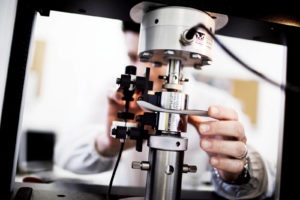
“Our customers include some of the largest companies in the world, who expect continuous improvement from their key supplier partners,” Brockman continues. “This means we have to continuously get better and bring enhanced value to our customers as the market demands stronger, lighter-weight materials that must perform well in ever-demanding environments. Customer value takes many forms, including rapid new product development, shorter production lead times and lower total cost of our products.”
Performance for health
The whole point of finishing textiles is to increase or enhance how the textiles function, so it’s no surprise that performance tops the list of client needs. “In the health care side of the market, most of the work is being done to develop cost-effective strategies for wheelchair cushions and mattress covers, to provide a softer, more comfortable surface as well as materials that are more waterproof,” says Jim Rose, chemical specialist at DAF Products Inc., Wyckoff, N.J.
Rose points out that there has been a significant move away from PVC-type materials, which are stiffer and less comfortable, and toward more use of urethane-based materials. “Urethanes are typically more expensive, but they lend themselves to an improved bariatric pressure gradient on the patient, so they lower bedsores and reduce discomfort,” he says. “They also match the body’s temperature more easily.”
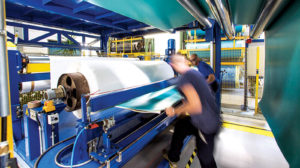
Standard vinyl products are still prevalent in many institutional settings, and cost and cleanability are factors that companies like DAF are addressing by “developing polyurethane-PVC blends to bridge the gap in cost but still provide comfort,” Rose says.
Trelleborg has also invested heavily in polyurethane lamination capabilities in the past five years. “Laminating technologies have enabled us to expand our offering of lightweight, air-holding products,” Brockman says. “We are continuously investigating new processing technologies, polymer chemistries and substrate materials, the creative combinations of which drive innovation.”
All fabrics welcome here
The newest advancement for TSG Finishing is the result of developing a technology with ever-broadening applications. In 2017, TSG launched DEFEND®, its high-performance textile finishing technology developed for the upholstery and wall covering market. DEFEND’s primary properties include high-performance water and stain repellence and are offered as either PFOA or PFC free. But TSG’s versatility allows them to also offer additional performance add-ons in the form of anti-abrasion/anti-pill, contract grade moisture barrier, microbe prevention/odor control, non-halogenated flame retardancy and commercial cleanability.
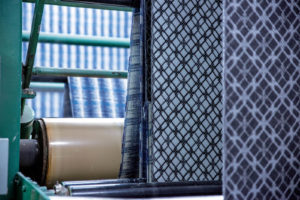
“The biggest difference with the DEFEND technology is that we’re able to put it on any fabric,” Rosenstein says. “I’ve challenged everybody I’ve spoken with about it to send me a piece of fabric that I cannot put our DEFEND technology on, and so far I’m batting a thousand.”
Perhaps the most surprising fabrics TSG has applied the technology to are velvets and embroidered silks. “The process we have allows us to put the technology on the fabric without crushing it,” Rosenstein says. “It’s a one-sided spray process that allows for drying in a relaxed environment—the fabric doesn’t have to be pulled tight to maintain tension.”
Of flammability and conductivity
For accredited test laboratories and research institutes such as the Bönnigheim, Germany-based Hohenstein Institute, advancement depends not only on its renowned core competencies, but
also on public funding. The institute received funding from the German government to conduct research
regarding graphene coatings.
“Graphene is a very new material and a promising carbon nanotube that has conductivity and [flame-resistant] properties, and we wanted to investigate those properties and whether they could be conferred to a textile material,” says Dr. Jan Beringer, scientific expert, life science and care at Hohenstein. “The initial findings from this project were that flammability and conductivity coating depends on the amount of graphene, so in principle, it’s workable. You can transfer properties from graphene onto textile materials. But there is a very high load of graphene required for the coating—up to 50 percent, so at that point the textile is not really a textile. It’s basically a plastic film or piece of wood.”
Beringer says the institute would like to continue working on the project, but its request for further grant funding is in process and it is unclear whether the grant will be awarded. In the meantime, there are some graphene coatings on the market for performance apparel, touted to disperse heat generated by the wearer’s body. “But the content of the graphene coating is far too low at the moment to have a perceivable difference between a graphene- and non-graphene-coated performance fabric,” he says.
Also on the conductivity front, Trelleborg has launched engineered coated fabrics to replace metal and metalized fabrics in a wide range of electrical management applications. Part of the fabric’s unique design is that it is omni-directional, meaning the conductivity is directional across the material. “Trelleborg’s new coated fabrics incorporate polymer chemistries and carbon-based fabrics that are resistant to corrosion, are flexible and are easy to fabricate and install,” Brockman says.
An ever-present tension
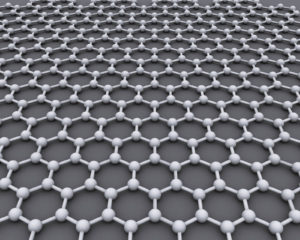
Second only to performance, sustainability is at the forefront of finishing companies’ development efforts. “For TSG, we’re in a bit of a different situation as a commission finisher, because we’re not selling chemicals to people. We’re providing a value-added service,” Rosenstein says. “The issue is that while my chemistry by itself might pass a certain environmental requirement, after it’s applied to somebody else’s fabric, it becomes a different component system and that system may fail.”
Rosenstein says that the type of oil or sizing used in the weaving process can affect the outcome, and that testing needs to occur on the finished products. However, he says “That’s impossible to do. You can’t test everything, so I believe a lot of people are making educated guesses.
“I like to educate people about all the possibilities,” he continues. “I know I lose market share sometimes because of that, but I want to be transparent.”
The CLI Group, located in Paterson, N.J., “is always upgrading materials and SOPs [standard operating procedures] to be more environmentally sensitive and compliant,” says Daren Silverstein, president. “All of our adhesives are waterborne and we recently upgraded our printing equipment to a latex system.”
This year the company also launched a new non-PVC wall covering system—GreenScape™—in response to increased demand for non-PVC products. The product is a non-PVC digital printable wall covering media manufactured with postconsumer recycled content polyester and other cellulose items. “It prints beautifully. It can be topcoated. And it’s green,” Silverstein says.
While the tension of creating finishings with increased performance and sustainability is a constant challenge, it’s also an opportunity for an ever-creative and solution-minded industry.
Sigrid Tornquist is a Minneapolis-based freelance writer and editor, and a frequent contributor to IFAI publications.
The need for nondisclosure agreements (NDAs) in product development is easy to understand. Whether verbal or written, they protect stakeholders from losing out on being the first to launch a new product or process. But they can also hinder marketing efforts and moving the industry ahead as a whole. Some comments by industry leaders on the topic:
Unfortunately nothing starts without an NDA—usually written, but it can be either written or verbal. But a level of trust is also important, and we have long-standing relationships with our clients and have an open dialogue with them about how to move a project forward.
Jim Rose, DAF Products
We do a lot of development work for other companies that we can’t elaborate on because of NDAs, but our end goal of course is to get the production work.
Daren Silverstein, The CLI Group
Most of the work Hohenstein does is funded by the government, so it’s public knowledge and we can talk freely about it.
Dr. Jan Beringer, Hohenstein Institute
Historically, the preferred way for us to do development was that nobody from the outside comes in the building—ever. We do have a tremendous amount of intellectual property to protect, but I do believe that that is an older way of doing business. I think developing partnerships with our customers and working with them as opposed to working for them is of tremendous value. As the fifth generation working in the company, I’m working toward breaking down those black box walls. It has to be done carefully, though. You can’t just open the doors like Willy Wonka.
Brian Rosenstein, TSG Finishing