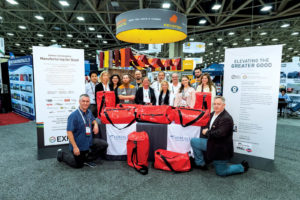
IFAI’s Manufacturing for Good booth made its second appearance at Expo 2018 held in October in Dallas, Texas. Workers at the live manufacturing booth assembled 74 red duffel bags from start to finish. The bags, made from 14 oz. vinyl, were donated to The Bridge Homeless Recovery Center, a North Texas-based organization devoted to helping its guests have access to a variety of services that are essential to their comeback from homelessness.
The Manufacturing for Good booth, which made its debut at IFAI Expo 2017 in New Orleans, La., showcased a portable factory on the Dallas show floor. Expo attendees were given a look at equipment demonstrations, sewing demonstrations and how the manufacturing process works from start to finish.
From idea to product
“When we read the personal stories of The Bridge homeless shelter and charity, we realized how homelessness could happen to just about anyone after a slight twist of fate,” says Christine Gerard, IFAI division operations manager. “We decided right away we needed to try and make a difference for the people of The Bridge.” When Gerard contacted The Bridge, community outreach coordinator Angela Jiura stated that “as one of the largest homeless shelters in the U.S., they would be happy to accept the duffel bags to help those in transitioning from homelessness.”
With a charity in mind, Gerard and Magda Ronningen, IFAI Makers and Equipment Division supervisor, began planning. Gerard assembled a design team of IFAI members: Roy Chism from The Chism Company Inc., Shane Cossette from TRS Industries, and Dave Elliott from David’s Custom Trimmers. Gerard, Ronningen and the design team pooled their manufacturing expertise to create a product design, a bill of materials and a list of necessary equipment to be shipped to the trade show for the live manufacturing event. The Chism Company Inc. adapted a pattern, created test samples and a work flow for the manufacturing, and each design team member contributed key manufacturing knowledge and expertise.
“They were a fantastic team of very busy business owners who dropped everything to help. Equally impressive were all of the sponsors and donors that stepped up to become involved,” says Ronningen.
Teamwork
The pop-up factory on the show floor provided Expo attendees with an up-close look at the stages required to manufacture the duffel bags. Processes highlighted included prototype development, patternmaking, pattern digitizing, automated cutting, prefabrication of shoulder strap and D-ring/webbing tab, grommeting, hot air welding, RF welding, sewing and assembling.
The booth was made possible through the efforts of numerous companies. This year’s sponsors included American Cord and Webbing, Autometrix, Custom Metal Crafters Inc., Edward Segal, Forsstrom High Frequency, FIL-Tec Inc., Groz-Beckert USA Inc., Herculite, Industrial Fabrics Foundation, Miller Weldmaster, Snyder Manufacturing Inc., TRS Industries, Value Vinyls, Vertilux, and YKK. Donors included Sunny Sewing Machines Inc. and Biothane, and sewers included Faith Roberts from Banner Canvas and Katie Bradford from Custom Marine Canvas.
Sammi Jones is an associate editor of Specialty Fabrics Review.