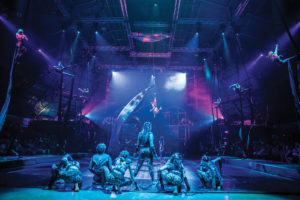
Fabricators go to great lengths to make sure every piece of material they produce or distribute will be up to difficult tasks. But sometimes the task is so specialized—or so extreme—that production requires a truly exceptional level of care, expertise and, often, regulation.
Products such as the ropes that firefighters use to rappel from helicopters and the parachutes that sport jumpers depend on to get them safely to the ground obviously require careful production.
“You don’t want a parachute ripping in half when it’s 6,000 feet in the air,” says David Mackney, vice president at Performance Textiles, a Wilmington, N.C., company that makes high- performance technical fabrics used for sport chutes, hot air balloons and other products.
For this article, we talked to manufacturers and distributors of these products to find out how such materials are created, the changing industry requirements, and what it takes to produce textiles used in extreme circumstances in accordance with stringent rules and regulations.
Skydiver fashion and function
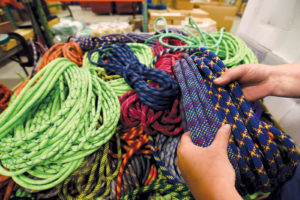
In the early days of skydiving, parachutes were made from a strong silk fabric, according to Mackney, but silk has long been replaced by ripstop nylon. “If it does rip or tear, it stops right there,” he says. “A 1-inch hole and it’s going to stay like that. It’s not going to continue to run, which is the last thing you
want in a parachute.”
Nylon may be the established standard for parachute fabric, but how that nylon is produced does change, for reasons of performance as well as aesthetics.
Mackney says that today’s sport jumpers increasingly want parachutes that allow them to descend at a greater speed but still land where they’re supposed to. That’s accomplished by using smaller canopies as well as fabric that meets appropriate porosity expectations.
“Jumpers use a different fabric than what the military might use to drop a truck from a plane,” he explains. “You can drop a truck anywhere in an area the size of a football field and it’s fine. But you’re a person, you want to drop dead center on the 50-yard line.”
Smaller chutes also play a role in skydiver fashion, says Ignatius “Kappie” Kapp, engineering manager for Performance Designs Inc., a parachute manufacturer in DeLand, Fla.
“We’re working with several companies right now to get fabric that actually makes the parachute pack smaller,” says Kapp. “It’s only about 15 percent smaller, which you may think is not a big deal, but it’s actually considered cooler to have a smaller backpack. If you could put your parachute in your shirt pocket, that would be the coolest.
“For some reason,” he says, “people think you are a student or not very capable if you wear something bigger on your back.”
In addition, different parts of a parachute have different requirements. Take, for example, the mesh fabric that is produced by Jason Mills LLC, in Milltown, N.J., which is used for the interior of parachutes.
“Our fabric has to be a specific pH,” says Mike Lavroff, the company’s president. “It can’t be too base or too acidic because it will start to destroy the nylon lining that it’s lying on, or the canopy itself. The fabric has to be as close to a neutral pH as possible.”
Hot air balloons
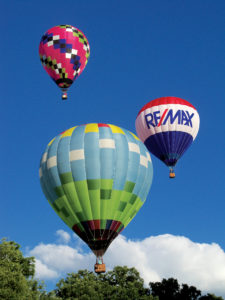
There are three main concerns with hot air balloons, according to Andrew Baird, general manager at Cameron Balloons in Dexter, Mich., the largest maker of hot air balloons in the world. Cameron built the Breitling Orbiter 3, the first balloon to fly around the world, and the Roziere 550 Spirit of Freedom, the balloon used for the first solo round-the-world flight.
“The fabric needs tensile strength, tear strength and it needs to be lightweight,” says Baird.
And as with parachutes, there’s the issue of porosity.
“A balloon needs to hold in all that hot air, and it needs to hold it as long as it can through its life span,” says Baird. “Today’s fabrics are far more resistant to porosity because coating technology has made great leaps forward. In the past, coatings would break down over time and the balloon would gradually become more and more porous, or less efficient in the way it flies. That really doesn’t happen anymore.”
Cameron produces a fabric called Hyperlast™, which is coated on both sides with silicone. The fabric is 30 percent heavier than conventional ripstop nylon, says Baird, but it’s up to 800 percent stronger.
Hyperlast was originally designed to be used in the upper portion of a balloon, which gets the most heat and UV exposure. “It makes sense to use a stronger fabric in that part of the balloon to get the most life from the aircraft as a whole,” says Baird. “But we’ve been seeing some commercial balloon operators who are flying passengers day in and day out switching to Hyperlast. It lasts longer, so it makes more sense in their business model.”
Advancements in technology don’t always come fast, but there’s a good reason for that, says Baird.
“Changing fabrics is a risky business,” he explains. “What happens in a lab or in weather testing machines doesn’t predict as much as we’d like about what will happen in the real world. The risk to us is that we introduce a product that tests very well in the lab, but we get it in service and five years later a problem shows up. Now instead of having a few balloons in service, we have five years’ worth.
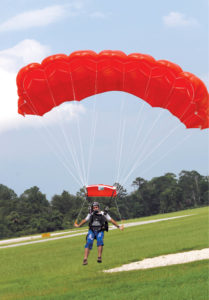
“Because we’re building aircraft,” he says, “quality is critical, so innovations tend to come more slowly, but more deliberately.”
There are also aesthetics to be concerned about.
“People who buy parachutes can get very picky about the color, simply because these things are so expensive,” says Mackney. “If you’re really into it, and you’re buying yourself a $3,000 or $4,000 parachute, you want that color to be perfect. You don’t want little spots on it from the dye or coating. It doesn’t impact the performance, but it’s aesthetically not pleasing.”
Innovations in ropes
Fabric is a critical piece of the rope descent systems manufactured by Sky Genie in Fort Smith, Ark., where they are used for a variety of purposes, including aerial firefighting and window cleaning on skyscrapers.
Those descent devices don’t work well with common “kernmantle” rope, which has an interior core protected by a woven exterior sheath. Instead, Sky Genie uses a rope woven from 20 strands of high-strength nylon fiber.
“Our rope works best with our descent devices because it is designed to have high knotability, which is a measurement of how tightly you can bend the rope,” says Sky Genie owner, Flip Kindberg. “A high knotability factor allows our rope to collapse on the descending device and causes the proper amount of friction that a kernmantle rope does not.”
The way rope is made—the weaving of strands to create a stronger rope—has not changed much, according to Kindberg. But fibers developed over the last 10 or 15 years have vastly improved rope strength and allowed more of a variance in a rope’s dynamic properties.
“In some situations, you want a rope that doesn’t stretch at all, such as when you’re lowering and lifting things,” Kindberg says. “But when it’s a human being on the end of the rope, you want some shock absorption designed into the rope. Rock climbers usually use a dynamic rope, so in a fall the rope is absorbing some of the impact, stretching to remove the snap.”
Technology has also allowed ropes to shrink in size and weight while maintaining the required safety characteristics, says Josh Walls, director of research and development for Sterling Rope Co. Inc., a Biddeford, Maine, company that makes ropes for both recreational climbing and work applications.
When Sterling was getting started, a small rope would have been 10.5 millimeters, says Walls, but some are now under 8 millimeters. “The evolution of the fibers used is what has allowed the diameters to shrink,” Walls says, “and new finishing and coating have improved to protect the fibers from both internal
and external abrasions.”
Safety regulations
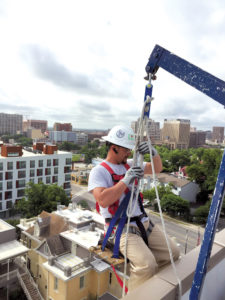
Not surprisingly, fabrics used in applications where safety is critical are subject to a raft of requirements, some dictated by government or industry standards, and some by internal specifications.
Sterling’s ropes, for example, are certified and verified by third parties, with specific certification depending
on the end use of the product.
“For climbing ropes,” says Walls, “we conform to UIAA 101, the standard of the International Climbing and Mountaineering Federation, which specifies minimum performance properties. All the testing is done in France.
“We’ve never sent a product that hasn’t passed,” he adds. “We know what the minimums are and we have the ability to test all of these properties in-house. It’s expensive to test, about $2,000, so we want to be 100 percent sure it’s going to pass.”
“There are quality checks at every point in production,” says Mackney. “Everybody who gets the fabric in the supply chain has checked everybody’s work along the way. The last thing you want to do is be the coater and you’re coating fabric that’s out of spec. You want to make sure of that before you coat it.”
According to Lavroff, the parachute industry uses the military spec Mil-C-3395 as a requirement in its production processes: “It’s a very useful tool that requires you do not exceed a specified weight as measured in ounces per square yard, and equally important, maintain or exceed specific strength requirements in regard to tensile and tear characteristics.”
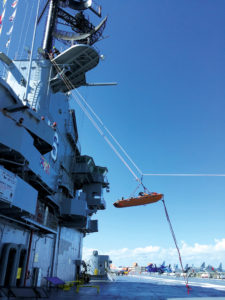
When it comes to products made by Cameron Balloons, says Baird, “Everything we do is according to approvals we have through the Federal Aviation Administration. We have engineering drawings approved for everything we build and a pretty lengthy quality control system in place to make sure we are manufacturing in accordance with those drawings.
“We are also periodically audited by the FAA,” he says. “They send a team in here and they can go through anything and everything in our building.”
Safety comes from regulation, but it also comes from people, Kapp adds.
“It’s unbelievable how well-trained the eyes of our in-house inspectors become,” Kapp explains. “What I like is that the people on our production floor are very compassionate. They don’t want anything to be made that could injure people. They feel very responsible for making something that will function 100 percent the way it is supposed to function.”
Jeff Moravec is a freelance writer from Minneapolis, Minn.
Until 20 years ago, “there were really no fabrics in the circus unless it was costuming or props,” says Dan Butler, co-founder (with his wife, Elizabeth “Betty” Butler) and executive director of Circus Juventas, a St. Paul, Minn., nonprofit performing arts circus school for young people.
But Butler says times have changed as the popularity of Cirque du Soleil and similar performing arts circuses have grown. Now, fabrics play a starring role in the productions staged by Circus Juventas, including its spring shows that feature 800 beginning and intermediate students, and summer shows featuring 100 advanced student performers.
“Cirque du Soleil kind of set the bar, and now we’re seeing fabric used in so many different things in the circus today,” says Butler.
Butler, who as a 15-year-old started under the big top of Sailor Circus in Sarasota, Fla., says prominent among the Circus Juventas acts that use fabric are those referred to as aerial silks, in which one or more artists perform acrobatics while hanging from long pieces of polyester material.
“Every circus calls it something different and they use different fabrics,” Butler says, “but there are just amazing acts that come from it. When it’s used in an aerial pas de deux act, with two pieces of fabric on a high-speed cable winch, the fabric becomes the safety device for the students because they wrap themselves in it. It’s quite an ingenious creation.”
Tricot and polyester materials with varying degrees of stretch are also used in several Circus Juventas acts, including those involving what is called a hammock, a single piece of fabric folded to make a loop in which single or paired artists perform aerial work.
There are also, of course, ropes that are used in a variety of acts. And while ropes have been around circuses for a while, advancements have been made. “That’s because of rock climbing,” says Butler. “As the rock climbing industry has sprung up, the circus has been able to embrace what they’re doing, particularly using ropes that come with specifications. That’s been a big change.”
Simulated golf is likely not on anyone’s list of extreme sports, but it is a sport that requires a fabric that’s pretty advanced—one that can absorb the impact of a golf ball traveling at more than 100 miles per hour and 3,000 to 10,000 revolutions per minute.
Obviously, the screen into which the ball is hit—which projects an image of the golf course—can’t be a traditional video screen material that could shatter. But there are other significant considerations as well, according to Mike Lavroff, president of Jason Mills LLC, in Milltown, N.J., which produces a line of heavy-gauge knit polyester materials that are used for the simulator screens.
“The screen needs to be durable and can’t pucker on impact,” says Lavroff. “Plus, it needs to have limited bounce-back and should deaden the sound of the ball.” It also needs to reflect a good image.
“The projectors have improved so much, and with high-definition (HD) images you can’t get away with the same materials you used five or 10 years ago,” says Lavroff. “For the higher-end units, we now use a tighter knit, and the imaging is incredible.”
The materials for the screens, produced to be marketed at various price points, cost from $20 to $50 per yard (at 120 inches), depending on the type of fabric chosen. Jason Mills is continually working to develop new and advanced materials that will integrate well with advanced HD and ultra HD images, according to Lavroff.
“Image quality and durability are the two big drivers in this market,” says Lavroff.